Industry 4.0 Smart Factory
The world’s industry is shifting to the direction of Industry 4.0. Industry has constantly evolved driven by new technology, from labor-intensive start to mechanization, from analogue to electronic machinery, computerization, followed by robotic arms and semi-automation.
Yet still, with market demands expanding, complicated and diverse, plus intense competition, industry is undergoing this latest round of adjustment, to improve production efficiency, flexibility and speed in meeting the customers’ need and serving the challenges of resource and energy, waste reduction, in light of global environmental concerns. Industry 4.0 is thus the future direction where the industries across the world are heading.
Cement-Building Materials Business which manufactures products for house and building construction is committed to transitioning its factories towards Industry 4.0 through the integration of technology and digitalization into all aspects of management and production. These include Smart Planning, Smart Operation and Smart Safety. No longer a factory full of workers and machineries, the new breed of factories is equipped with Internet of Things (IoT) connected devices, robots and automation systems operated and controlled by AI/Machine Learning and Big Data to optimize production efficiency while using less resource, energy, generating less waste, in compliance with standards and targets.
Smart Planning
Cement-Building Materials Business serves manycustomers across Thailand, whose needs are different interms of product types, volume and timing of delivery.To respond to customer’s requirement with in-timedelivery, the production planning is the most crucial step.Previously, the process was carried out by staff usingcomputer software to analyze data, factors and variablesto make decisions on the production plan based onthe available capacity of factories and machineries.The approach incurred risk of mistakes, time-consumingand lacked of flexibility to cope with customers’ requestto change orders.
Cement-Building Materials Business collaborated with Department of Mathematics and Computer Science, Faculty of Science, Chulalongkorn University, in developing
CAPOM — Cement Allocation and Planning Optimization Model for efficiency of cement production planning. As smart planning platform, CAPOM plans for efficient production, reduced energy cost and logistics cost as well as quicker planning period. The artificial intelligence system (AI) generates demand forecasting to optimize cement production, based on inputs of relevant data sets including stock and machinery status at the factories through cloud computing. The AI system enables Cement-Building Material Business to match customers’ requirement with factory production capacity, reduce loss of production and logistics, and run operation continually while managing stock and inventory against deficit nor excess. CAPOM assists in scheduling factory daily production, boosting precision and efficiency in every step along the way.
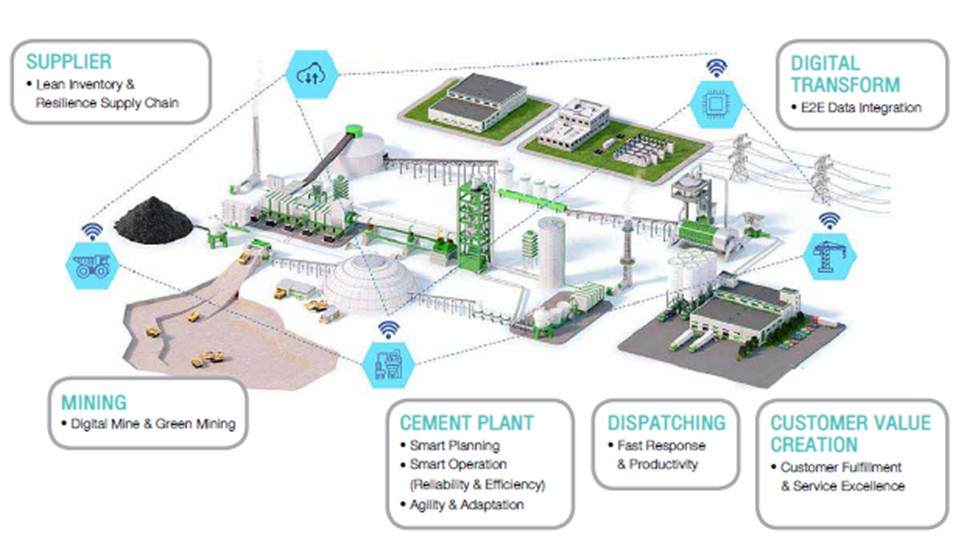
In 2021, CAPOM Smart Planning has been deployed at the cement plant, Kaeng Khoi, and help speed up the production plan by 75%. The plans are underway to scale up deployment of CAPOM Smart Planning to other cement plants of SCG while the system itself is being further developed to connect Smart Planning and Smart Operation for an end-to-end smart system.
Smart Operation
Precision, Speed, Higher Productivity, and Less Loss Production process involves multiple steps through product lines that starts with processing of raw materials until the final outcome of beautiful and functional products.
In every single step, multiple variables need to be well managed, including precision control of machinery, inspection of product from each production unit for quality assurance before passing onto the next step to reduce loss from substandard outputs at end line. Complex production control undertaken by human is susceptible to risk of mistakes, machinery glitch and faults that may be unnoticed, resulting in damaged outputs or production shutdown from an unanticipated downtime.
Optimization of production efficiency inevitably needs Industry 4.0 automation technology, in tandem with upskilling of human resources to be capable of digital technology to support operations across production units. Cement-Building Materials Business began developing Smart Operation in concrete roof factory by replacing the entire set of machinery and introducing AI/automation system, robot, IoT and AI devices. These machines and devices communicate via digital platforms to control machinery operation and production. Manufacturing Execution System (MES) in the VA Room (Visualized & Analytics Room) is the central operating system to enable the control of machines in every single production unit and manufacturing time. Efficiency is monitored from real-time data visualization dashboard. The system monitors the condition of machinery, data, temperature, humidity and other variables for production efficiency analysis and trouble shooting.
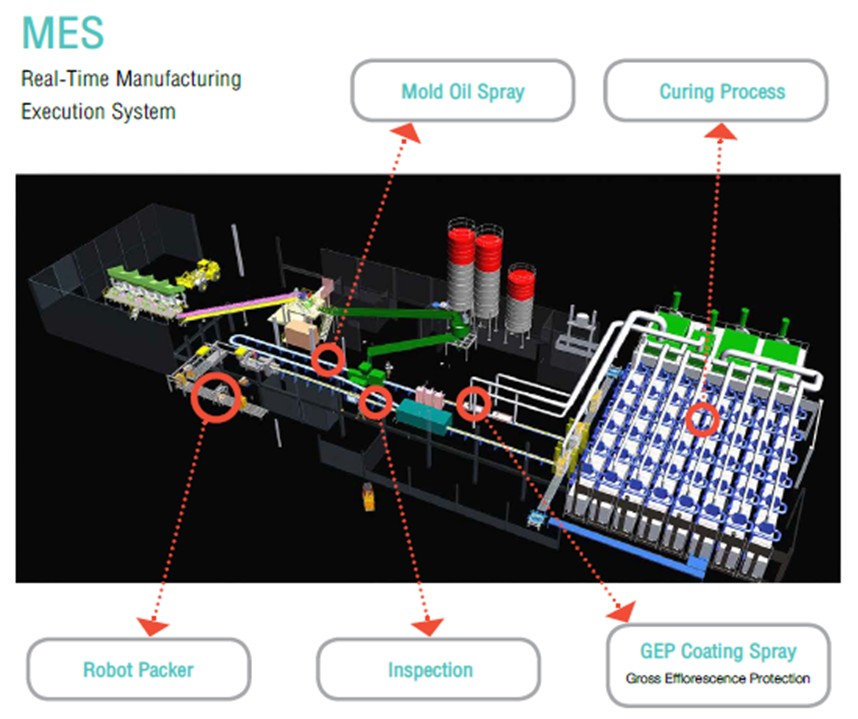
Furthermore, AI and Image Processing technology provide automated inspection system of fault finding in multiple stages of the production process starting with the stage of mold oil spray prior to shaping of tile to reduce problem of uneven coating, the stage of tile color spray (GEP coating spray) to ensure even coating and avoid defect products, as well as the stage of inspection to detect the defects and automatic reject out from the production line. This was done through knowledge transfer of Image AI from the cement plant.
Outputs that meet quality will then be handled by automate handling, which moves pieces in and out of the curing room, and robot packer shall pick up products for packaging.
For inventory management, the Warehouse Management System (WMS) is an operating system using QR Code for information and space management to reduce errors between loading staff and delivery staff to ensure correct delivery.
The implementation of AI jointly with automation in managing different functional areas inside a factory enables an efficient flow of production lines with precise monitoring system, increased productivity within the same amount of time, optimized resource use, energy saving and less labor dependence for safe work. In addition, there is a notification system on equipment status and machine capabilities for maintenance schedule.
Cement-Building Materials Business uses Overall Equipment Effectiveness) (OEE) to measure manufacturing productivity of Smart Operation against world class benchmarking in terms of ability to reduce losses from downtime, speed and quality.
In 2021, Smart Operation has been implemented at two roof tile factories, and planned to rollout in all six factories. The manufacturing productivity through OEE score increases from 53% to 78%, increased outputs to over 8.5 million pieces per year, and decreased reject to only 1.5%.
Smart Safety
Protect, Monitor and Safe
Although the factory deploys digitalization, AI, robotics and automation systems, the workforce is needed to jointly inspect production processes and feed data onto digital devices. In this setting, Smart Safety is an important element of a Smart Factory for safety of workers and contractors working on site.

Targeting to zero occupational illness and injury, Cement-Building Materials Business developed Smart Human Tracking that is already implemented at the cement plant, Khao Wong. The system tracks location and status of worker through a signal transmit device installed atop of safety helmet. Data are fed real-time into the system inside the control room. In case of emergency, a worker can press the alert system button for prompt assistance. The system also helps manage overall safety arrangements inside the factory by tracking and controlling entry and exit at different areas. Disaggregated data are displayed according to categories such as staff, suppliers/contractors, or visitors. It also alerts in case of unauthorized access or access into unsafe zone.
Smart Human Tracking also helps boost efficiency of employee caring during the COVID-19 pandemic, when physical distancing is a measure to prevent the transmission.
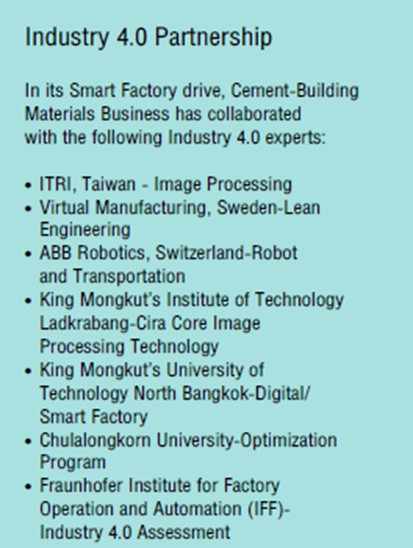
………..
Industry 4.0 is a challenge for Cement-Building Materials Business in terms of new technology investment, worthwhile benefits and expected performance. In quest for the right technology, the Business has to collaborate with relevant partners to create innovations for practical and efficient deployment. And above all, the important aspect is to reskill and upskill the workforce with technological literacy in order that they can perform in the Industry 4.0 way of work.
Cement-Building Materials Business is in readiness to drive its business across the supply chain towards Industry 4.0 for SCG’s sustainability.