Zero Burn Creating Renewable Energy while Reducing Pollution from Straw Burning
Every year between March and April, there is the post-harvest period in paddy fields everywhere
throughout Rangjarakhay Subdistrict of Sena District, Ayutthaya Province. Local rice farmers
said they had no other choice but burning the straws after harvesting their first crop of rice. The
one-month window between post-harvest in April and second cropping in May is too tight for the traditional practice of leaving straws to decompose on the field itself which requires more than two weeks. Locals here prepare the field for annual second crop by burning out the straws.
Similarly, farmers across Thailand clear their fields of waste such as sugarcane leaf, corn cob and straws
by burning. As a result, Thailand has been living with air pollution from various sources like smoke, smog, PM 2.5 particles, global warming and other health consequences.
Now the idea of helping famers to maximize the resource use, utilize straw and other agricultural waste
instead of just burning is being implemented according to the circular economy principle.
Rangjarakhay Move Forward to Zero Burn
Cement-Building Materials Business launched the Zero Burn initiative through purchasing of agricultural waste from end of 2019 in areas around SCG’s five cement plants located in Saraburi, Lampang and Nakhon Si Thammarat Provinces. Purchase points are being added among CPAC ready-mixed concrete plants which located in every part of Thailand.
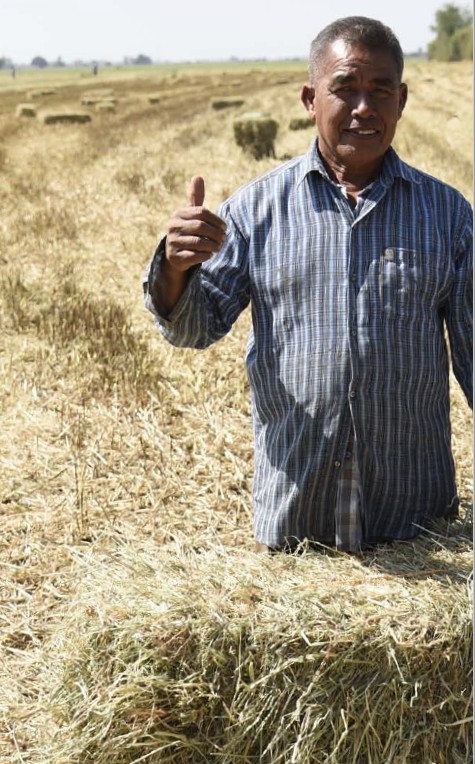
The purchase scheme focuses mainly on paddy straw, sugarcane leaf and corn cob, to be used as feedstock to make energy pellet for cement kiln, substituting coal as fuel. In the case of rice straw, if a purchase point is located very far away from a cement plant to the extent that transport cost does not make economic sense, machineries are deployed for straw shredding and compressing into energy pellet, which are smaller and more compact, for haulage of 20 tons per trailer.
At Rangjarakhay Subdistrict in Sena District, burning left overs is a dilemma with which farmers have been struggling for years. Driven by a sense of urgency among the local people, the Subdistrict Administrative Organization collaborated with SCG in implementing the initiative, and
entered into partnership with Siam Kubota Corporation Co., Ltd. which donated two straw compressing vehicles to be used in the project.
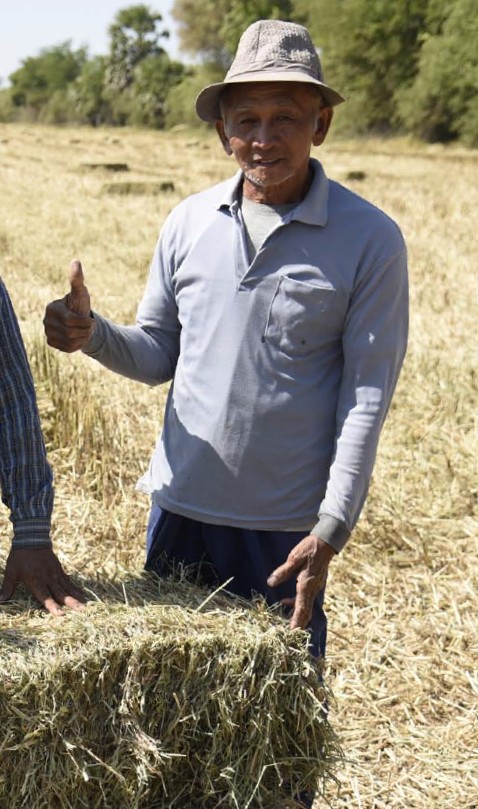
For the purpose, SCG set up an energy pellet factory, its first, in Lad-nga Subdistrict adjacent to Rangjarakhay. The factory provided crucial support to Zero Burn Scheme in Sena District. Farmers can transport straw bales to the factory, to be transformed into energy pellet, which will then be hauled to feed as fuel to The Siam Cement (Kaeng Khoi) Co., Ltd. and The Siam Cement (Ta Luang) Co., Ltd.
(Khao Wong Plant), Saraburi province, located about 100 kms from the site.
“Thanks to the irrigation, at Rangjarakhay, we can grow crops of rice twice a year. In the past, burning was only way because it’s quick. When we finished the first crop and preparing for the second, there is not enough time to decompose the straws. The second cropping must complete before floods arrive towards end of the year,” said veteran farmer of Rangjarakhay, Waraporn Chalermsilp.
“The good thing about this project is that villagers no longer have to burn straws and this is how we help reducing the pollution. The Chief Executive of the SAO (Sub-district Administrative Organizations) helped us earn additional income from selling straws. But it is worrying that here there are thousands of rai of rice fields. Each plot would finish harvesting around the same time. Our concern is that the straw compressing tractors might fail to keep up with the ever increasing volume.”
Waraporn and her friends shared the view that if the two existing compressing tractors can roam around and process 60-70% of post-harvest straws, they are optimistic that seasonal burning activities would be scaled back each year.
Pongsakorn Mongkolmoo, Chief Executive of the SAO, is aware that PM 2.5 pollution is a national problem. “Here we campaign for farmers to cooperate, urging them not to burn straws. But if we don’t offer them option or equipment, most of them would still continue to burn. That’s why we sought SCG’s support, in installing the straw-compressing machinery onsite. We also received support from Siam Kubota with the tractors. With these, we believe we can achieve 100% reduction of straw burning.”
Straw Haulage
The sky was bright blue, the air cool and windy during year-end cool season. From the road shoulder, the whole landscape is dominated by flat rice fields. By the roadside two red Kubota tractors were hauling straw compressing machine along the stretch of the road. Stubbles, straws and farm waste were everywhere. When the vehicle moved, straws would be sucked in, compressed and out came square bales along the carousel at the rear of the tractor. Workers use steel hooks to move them to assemble at one
corner. Each straw bale weighs between 18-20 kilograms.
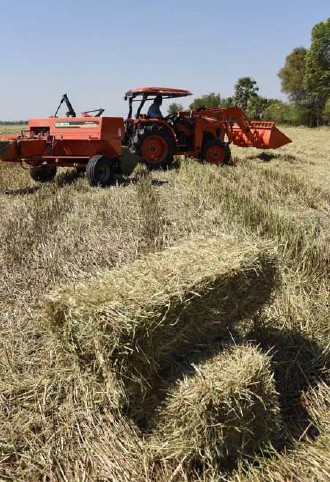
Wicha Kerdpun, age 70, owner of this rice field, said since last year he felt a very strong urge to resist burning, to the extent he was willing to pay haulage of straw from his farm for disposal somewhere else.
“I have a total of 100 rai, and this plot alone is 14 rai. I am the first in Sena District to have paid for straw haulage. I paid 5,000 baht for the service, plus offering lunch for the driver and the crew. If burning is illegal, then it gives me peace of mind to pay for this,” Uncle Wicha laughed at his own thought. “Like some projects told us to leave rice straws to decompose naturally. That’s time consuming and people who say so and those who actually work the rice fields are different people. They have no idea what it’s
like. The Zero Burn project hits the nail in the head, addressing the problem spot-on.”
“You just let us know, we will be here, compressing straws for you and buying it at 50 baht per rai,” added
SAO Chief Pongsakorn. “If this project turns profit, we will share it back to farmers in various forms.”
Pongsakorn explained that the Subdistrict Administrative Organization would make straw bale, and after SCG purchasing the outputs, farm owners will be paid 50 baht per rai, with parts of proceed allocated for expense and public interest fund such as scholarship for poor and needy students, or farmers’ welfare. The fund is set up and managed by the villagers themselves as a community based enterprise with SAO as mentor. In the step to follow, bales are transported for energy pellet processing at SCG factory located in Lad-nga Subdistrict some 20 kilometers away from this field.
Straw Compressing
The energy pallet processing plant is located on a site owned by CPAC in Lad-nga Subdistrict, known among local people as the “sand pit”. Outside the factory is a vast open ground with piles of straw bales.
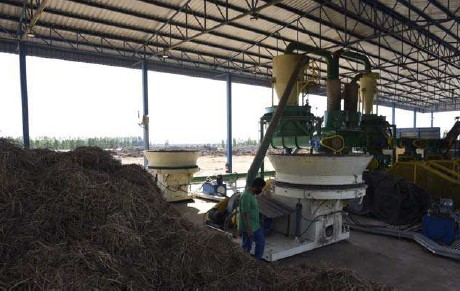
SCG employee Warawut Samermuan told us that “this factory started operation in May 2020. All that you
saw was the result of first haulage in February 2020. We gradually processed them and deliver to Kaengkhoi cement plant in Saraburi.” Warawut explained that when bales were delivered here by farmers, the factory staff must measure the moisture level, which must not exceed 25% to be purchased. “Workers have to use hooks to winnow and puff up straws before they can be fed into the machinery.” Once processed, each pieceof straw would measure around 24 millimeters, to be sucked and fed into the pellet maker. Outputs are both smaller and higher bulk
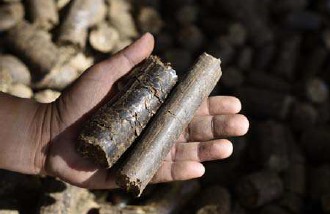
Schwinn Chattaris is another SCG worker closely involved in the project, as systems design engineer for
the factory supervising production process. “The challenge is that raw materials such as straw or sugarcane leaf are light-weighted, making haulage uneconomical. We have to find ways to process, slicing and compacting into smaller masses to make for transport volume. We studied technology, machinery design and installation. We are experimenting a variety of approaches. Three teams are working together: the procurement team to source raw materials from farm waste, the second team is the customer co-development, working to produce biomass from agriculture waste and maximization of use and value from the cement plants and external clients; and the team I am in charge of that is the technical team. My team is in the middle, receiving problems from two other teams and find the right
technology to process raw materials into biomass that customer wants.”
Schwinn said in the near future the factory aims at producing 0.5 ton of biomass per month, and increasing in the next step to 1.5 tons per month.
Scaling Up for All
SCG has plans to increase purchasing points of agricultural waste through its network of CPAC plants nationwide and it sets the target of producing biomass to substitute coal import to the tune of 1 million ton per year.
There are many ways to reach the target, such as setting energy pellet factories in a number of other locations, exploring collaborative partnership along the line of OEM approach with machinery-owning partners to produce energy pellets.
In addition, SCG has the idea to promote and support community-based factories that are using small machineries across Thailand to venture into this undertaking in the form of community-based enterprise. “We believe that Zero Burn project is beneficial,” Schwinn said with confidence. “From business case perspective, we use low-cost materials to make biomass. In another perspective, we add value to waste. It’s exhausting yet challenging: the change of perspective, in relations to machinery, people, and cement
business.
Everybody must change, adapt and in the end the whole chain improves. Farmers get more income, truck
drivers have jobs, cement plants use less coal and more biomass. I am proud to be part of this advocacy to turn agricultural waste to renewable energy.” Schwinn’s sense of pride is shared by other SCG employees taking part in the Zero Burn project that helps reduce environmental problem and serve the interests of multiple sectors within the Thai society.